Casting Aluminum Mastery: Unleash Your Creative Potential
Casting Aluminum Mastery: Unleash Your Creative Potential
Blog Article
Opening the Possible of Aluminum Casting: A Comprehensive Introduction
Light weight aluminum casting stands as a keystone in the world of metalworking, using a plethora of advantages and applications throughout various sectors. From its historical significance to the modern-day technologies in casting methods, aluminum has continually verified itself as a important and functional product. As we navigate via the landscape of aluminum casting procedures and explore the details of quality control measures, a thorough summary of unlocking truth possibility of this steel emerges. The opportunities appear limitless, promising insights that can transform the way we make use of and perceive light weight aluminum in manufacturing (casting aluminum).
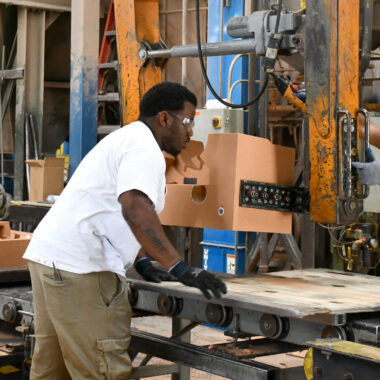
History of Aluminum Casting
Light weight aluminum spreading has an abundant historical history that goes back to old human beings, showcasing the withstanding significance of this metallurgical process in various sectors. When ancient civilizations like the Egyptians and the Sumerians made use of basic approaches to cast small things, the roots of aluminum casting can be mapped to around 5,000 B.C.. It was not until the 19th century that aluminum spreading saw considerable advancements with the exploration of the Hall-Héroult process for extracting aluminum from its ore, making it much more available for casting functions.
The adaptability of light weight aluminum casting enabled for intricate forms and elaborate designs to be created with precision, better fueling its fostering across different sectors. Today, aluminum casting continues to be a cornerstone in the production of a large range of products, highlighting its enduring heritage and value in modern production procedures.
Applications and advantages
With its extraordinary strength-to-weight proportion and superb thermal conductivity, aluminum spreading provides a myriad of advantages and varied applications across numerous markets. One of the key benefits of aluminum spreading is its lightweight nature, making it a suitable option for markets where weight reduction is critical, such as automobile and aerospace.
In terms of applications, light weight aluminum casting is commonly used in the automotive sector for parts like engine blocks, cyndrical tube heads, and wheels due to its stamina and lightweight buildings. The convenience of light weight aluminum casting extends to customer electronic devices, where it is used in the production of housings and heat sinks.
Types of Aluminum Spreading Procedures
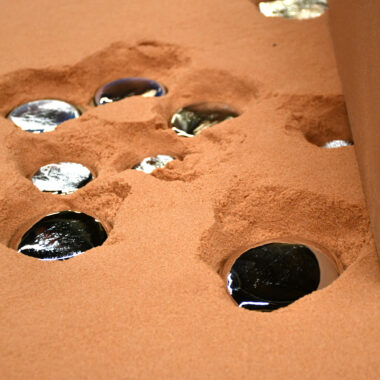
Amongst the numerous techniques used in commercial setups, aluminum spreading procedures incorporate a range of strategies matched to various applications and requirements. Investment casting, also recognized as lost-wax spreading, is preferred for its capacity to create comprehensive and complex components with a smooth surface coating. Each of these aluminum casting processes supplies unique advantages, providing to a broad variety of commercial requirements.
Innovations in Light Weight Aluminum Spreading Strategies
Current innovations in light weight aluminum casting strategies have actually changed the manufacturing market, supplying improved effectiveness and precision in the production of facility components. One notable development is the development of 3D sand printing innovation, which allows the creation of detailed sand molds with marginal manual work. This technique permits greater design adaptability and faster manufacturing cycles, making it optimal for prototyping and tiny batch manufacturing.
Moreover, using sophisticated simulation software has actually substantially boosted the spreading procedure by making it possible for engineers to optimize mold and mildew designs and predict possible flaws before production begins (casting aluminum). This leads to enhanced item top quality and minimized material waste
In addition, the adoption of vacuum-assisted aluminum spreading has actually improved the general top quality of castings by decreasing porosity and guaranteeing a much more consistent circulation of liquified steel. This technique is particularly beneficial for parts that need high structural integrity and exceptional surface coating.
Quality Assurance in Light Weight Aluminum Spreading
The advancements in light weight aluminum casting methods have not just improved efficiency and accuracy but have also underscored the crucial significance of quality assurance in making certain the reliability and performance of actors components. Quality assurance in aluminum casting involves a methodical technique to assess the manufacturing and monitor process, determining any type of deviations from established standards that could influence the last item.
One critical aspect of high content quality control is the usage of innovative innovations such as non-destructive screening methods like X-ray and ultrasound to spot inner issues without jeopardizing the integrity of the actors components. In addition, implementing strenuous assessment methods at numerous phases of manufacturing assists in determining and remedying concerns immediately, guaranteeing that just components satisfying the defined requirements are released for usage.
Additionally, quality assurance prolongs beyond the production process to incorporate post-casting treatments like warm treatment and surface area finishing, ensuring that the final items satisfy the wanted specifications. By prioritizing high quality control procedures, suppliers can boost item consistency, longevity, and general customer complete satisfaction in the world of light weight aluminum casting.
Conclusion
Various kinds of casting procedures and cutting-edge strategies have actually been created to improve the efficiency and quality of aluminum casting. On the whole, light weight aluminum casting proceeds additional hints to be an important production procedure with great prospective for more innovations in the future.
As we navigate through the landscape of aluminum casting processes and delve right into the ins and outs of high quality control measures, a detailed introduction of unlocking the real possibility of this metal emerges. It was not till the 19th century that light weight aluminum spreading saw considerable advancements with the exploration of the Hall-Héroult procedure for drawing out aluminum from its ore, making it much more accessible for casting purposes.
Among the numerous methods utilized in industrial setups, light weight aluminum spreading procedures incorporate a variety of methods suited to different applications and requirements. Financial investment casting, likewise recognized as lost-wax spreading, is favored for its capability to generate in-depth and elaborate components with a smooth surface finish. Different types of go casting procedures and ingenious methods have been established to boost the efficiency and high quality of aluminum casting.
Report this page